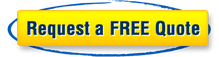
Describe the SIPOC Process in Lean Six Sigma
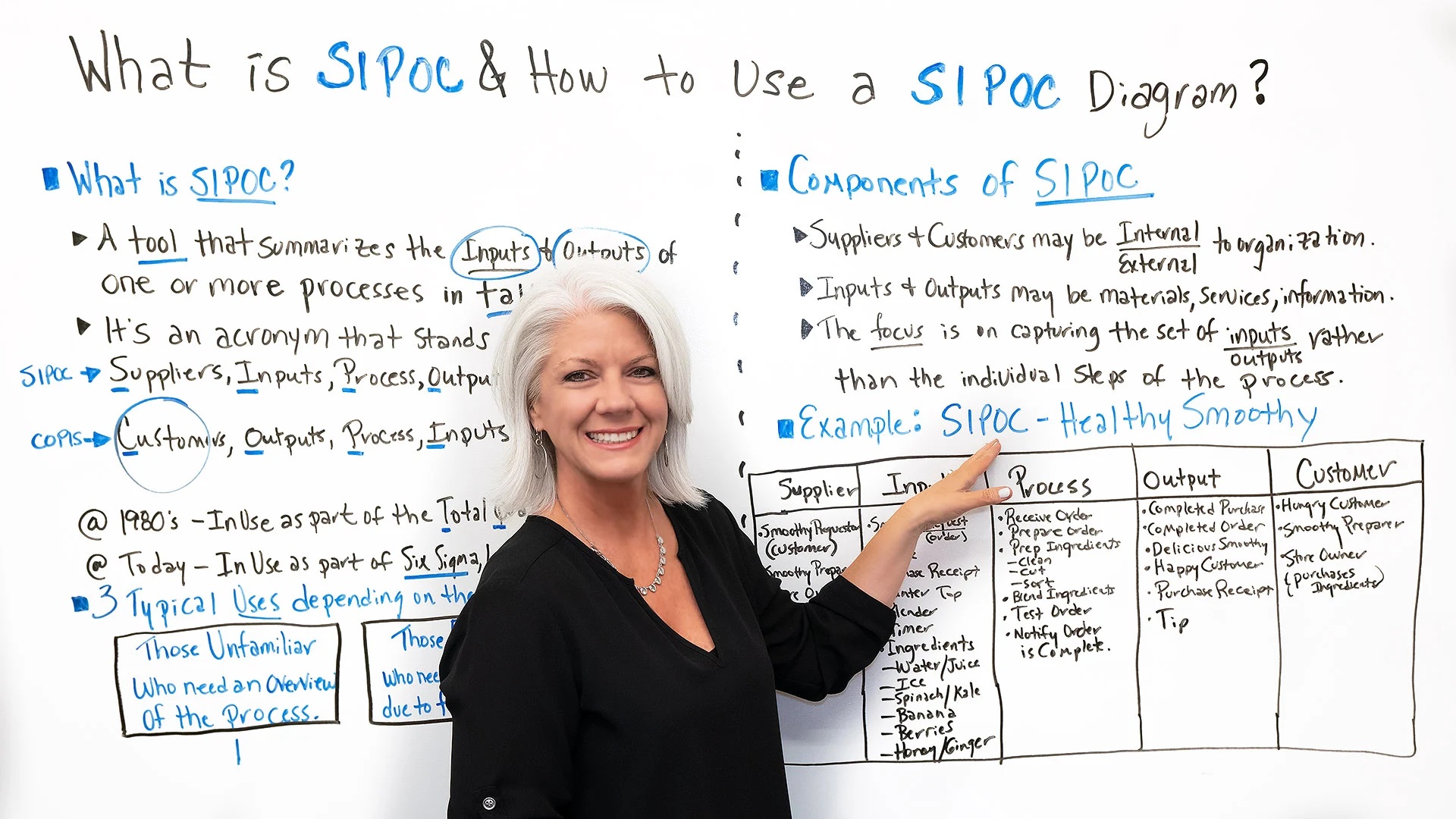
The business world can never experience a shortage in all the different techniques, strategies, and tools to help them grow, develop, and expand their businesses. Lean Six Sigma has been one of the most prominent and the most sought after because of the versatility and the overall flexibility of it.
If you are just new to Lean Six Sigma, then all of the terms and the jargons might confuse you. To be able to understand it correctly and efficiently, we first need to define what Lean Six Sigma is, how it’s helpful to companies and businesses, and the like.
Quick Explanation of Lean Six Sigma
Lean Six Sigma is known by many – if not all businesses that use it – as the problem-solving methodology that uses data, graphical, and statistical analysis depending on the results and the outcomes you are looking for. It helps companies to become better and more developed and everything it has is aimed to improve and develop business procedures and processes.
While Lean Six Sigma imposes a ton of different benefits and outcomes, its clear goal is only to be able to provide a continuous and a well-planned series of procedures that would heighten and increase the customer experience and satisfaction by clients.
Lean Six Sigma Tool: SIPOC
Among the many tools you can use for Lean Six Sigma, the SIPOC tool is considered to be the driver of success as it tackles everything that’s needed – from data, process planning, execution, and the like.
There are others such as the DMAIC and DMADV, the Kaizen Method, the Five S’s, and many more, but the SIPOC tool is comprehensive and it would absolutely lead to the success of any project.
The SIPOC Model
How is the SIPOC tool used in business strategy and improvement processes? Can companies use it effectively and productively to arrive at the results they are looking or yearning for? How would you Describe the SIPOC Process in Lean Six Sigma?
Answering all those questions would only require the definition of the SIPOC model and what its abbreviation stands for. It’s a process that contributes to the next level – without the main category or the Supplier, the SIPOC methodology wouldn’t be possible.
Suppliers (S)
Whatever industry or sector you operate in, the SIPOC methodology or process would need data from your suppliers. This procedure would require the recognition or the identification of the suppliers or who provide the inputs to your customers or your clients.
Inputs (I)
Following the suppliers would be the Inputs. What are the specific things, products, or services do you offer your customers? What information or data are to be used in the process? It’s relevant and essential because it would track down and type of inconsistency that your business operations may have.
Process (P)
The Process is the heart of the SIPOC methodology – it is the phase where the process of how a certain product is produced or how a service is done and completed is discussed in detail. More often than not, this translates to as manual instruction – a step-by-step narration of how a certain result is achieved.
Output (O)
After going through the suppliers, inputs, and the process – the outputs process is what will matter the most because it’s what clients and customers would rate and give feedback to. After ample time of investment, the end product would be determined in this and this will reflect your effectiveness and efficiency as a business.
Customers (C)
Customers aren’t only the people you sell your services or products to – sometimes, our clients and customers are our business investors, stake, and shareholders. To put it simply, customers are people who have no say on how your business is run but would benefit from you doing your business correctly or appropriately. Your investors and stakeholders, at this point, can gain more profit if you do it in the best ways you can. Your market or your clients, on the other hand, would be able to get the best and the highest level of products and services.
Can You Use SIPOC?
If ever you’re questioning the effectiveness of the SIPOC model or tool, and if you are doubting whether or not it will be effective in your sector or your industry – do not. The SIPOC tool is a flexible and versatile tool that is used and utilized by businesses and organizations so that they are just on the path to success. It can identify all the hidden failures that it can impose on your projects – and the SIPOC diagram can give you the foresight on what you need to prepare for in the event that something wouldn’t function properly and appropriately.
Herewith us at Lean Six Sigma Curriculum Experts, you can get the chance to work with the best and the most skilled in the SIPOC Process. Whether you need further training on what it is, or how it can be used as a defense against failures and errors, you can count on us.
The Most Experienced Professionals
Out in the industry, there’s no other team that can help you the way we do. We have been the most trusted organization that carried out Lean Six Sigma Training and Certification services; you will never regret your decision of working with us.
Not only are we the best because of our people – we have also designed and streamlined our processes and procedures to be highly efficient and effective no matter where you are in the supply chain.
Through the command we have over the SIPOC process, it’s only a matter of time until you fully understand and comprehend the process. Lean Six Sigma Curriculum Experts is the company or the organization you can count and bank on if you need deep knowledge over a particular business process improvement method.
Dial us via our hotline or send us an email – you will get the best and the highest standard of Lean Six Sigma Training you will find in the market. Be well-versed in the SIPOC Process in Lean Six Sigma without burning a hole in your pocket!